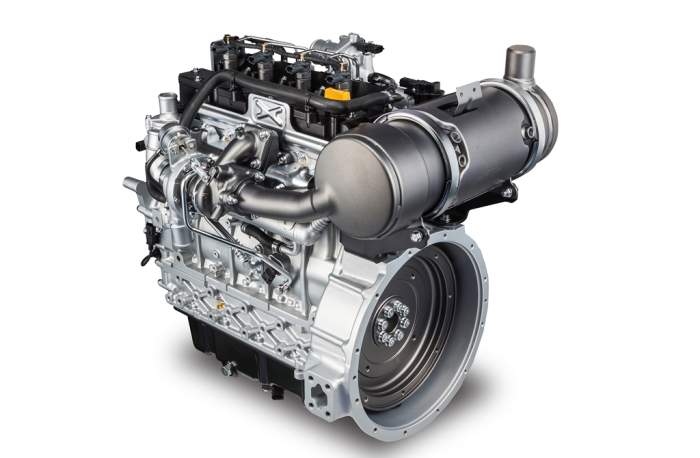
- Share
What is Industrial Engine Break-in?
All engines require some type of break-in. Although current technology provides the means of manufacturing engine parts with excellent precision, the manufacturer still falls short of achieving the near-perfect fit that a proper break-in would.
Industrial engine “break in” is the allowance of the machined cylinder and ring surfaces to conform to each other's shape during engine operation.
A tight seal is important because it prevents the escape of unburned fuel and pressurized gasses into the crankcase, while also preventing crankcase oil from getting into the combustion chamber, which is the ultimate goal of a proper break-in.
During break-in, small amounts of oil consumption will occur, which is perfectly normal and acceptable in new engines. Although acceptable at first, these attributes must not continue after the break-in has been completed.
For break-in to occur, a fair amount of heat, friction, and resulting wear will need to take place before the piston rings have “mated” with the cylinder walls. Running the engine under very light or no load prevents the oil film on the cylinder wall from being scraped away by the piston rings.
Eventually, this leaves a hard deposit on the cylinder wall known as glaze. The rings never set well if they cannot expand from the dynamics and heat that a load produces. One can expect continuous oil consumption, poor mileage, and increased bearing and engine wear for the entire lifespan of the engine.
When new, a modest amount of heat is created merely from the friction of the new rings passing over the freshly honed cylinder wall. While significant, the real heat is created from the combustion of the fuel. When the fuel is burned, combustion gasses expand and heat all of the cylinder parts.
Moderate loading will introduce more fuel to the cylinder and add significant amounts of heat and pressure to the cylinder components. A recommended loading of 70% to 80% (of the engine’s power rating) is common. Moderate loading is the key to a proper break-in, usually lasting the first 150 hours. Noticeable improvements in fuel economy or the “character” of the engine are also good indicators.
Some recommended Dos and Don'ts include:
Don't - run the engine hard for the first few hours of operation. It is recommended that the engine be operated around the peak torque. This loads the engine gently and predictably.Don't - let the engine idle for extended periods during the first few hours of operation. As previously stated, running the engine under very light or no load prevents the oil film placed on the cylinder wall from being scraped away by the piston rings.
Do - operate the engine under moderate loads at varying RPMs until around the 10 to 15-hour mark. The idea is to alternately heat and cool the rings under varying RPMs.
Do - begin to put a heavy (using almost the entire engine’s working capacity) working load on the engine at around 15 hours and get the engine hot. Keep the revs up and make sure the coolant temps rise. After 15 hours of heavy working load, begin operating the engine under moderate loads again, making sure to let the engine get up to normal operating temps (no light work cycles). Monitor gauges erring on the side of caution.
For more information, contact our power systems specialists to discuss your diesel engine options.